Tool Steel Supplier
Tool Steel D2, 01, A2, EN24T, H13, P20
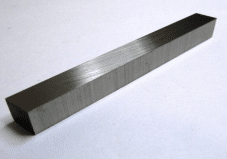
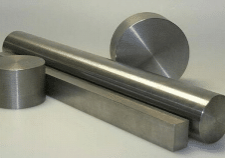
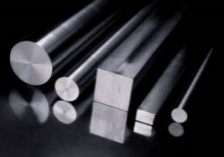
The One Stop Metal and Plastic Shop
Order tool steel from Jade Metals today for top-quality, industry-standard materials. Our tool steel is known for its exceptional hardness, wear resistance, and ability to hold a cutting edge, making it ideal for manufacturing tools, dies, and moulds. Whether you're in metalworking, machining, or another demanding industry, our tool steel options will provide the durability and performance you need. At Jade Metals, we ensure fast service, reliable delivery, and materials that meet the highest industry standards. Place your order today by giving us a call and let us supply the tool steel you can depend on for precision and strength.
D2 Tool Steel
D2 tool steel is a high-carbon, high-chromium, and semi-stainless steel known for its excellent wear resistance, toughness, and durability. It belongs to the cold work tool steel family and is commonly used in various industrial applications where cutting, forming, or shaping materials at room temperature or slightly below are required. It's important to note that D2 tool steel is not suitable for applications requiring high levels of corrosion resistance, as it can still be susceptible to rust and staining when exposed to corrosive environments.
01 Tool Steel
O1 tool steel is a popular and versatile oil-hardening tool steel known for its excellent wear resistance, toughness, and ease of heat treatment. O1 steel has good dimensional stability during heat treatment, minimizing the risk of distortion or warping. It's commonly used in the manufacturing of a wide range of cutting tools, such as knives, chisels, plane blades, and various types of punches and dies. This tool Steel is readily available in various forms, including sheets, bars, and custom-made tooling components.
A2 Tool Steel
A2 tool steel is known for its exceptional wear resistance, making it suitable for applications where tools and components are subjected to abrasive wear. A2 steel is an air-hardening steel, which means it is quenched in air to achieve its full hardness. The steel is heated to its critical temperature, followed by air quenching, and then tempered at various temperatures to achieve the desired hardness and toughness characteristics.
EN24T Tool Steel
The tensile strength of EN24 in the T state is typically 850/1000 N/mm2. Due to its outstanding machinability in the "T" condition, EN24T steel is a well-liked through-hardening alloy steel grade. EN24T, whose hardness ranges from 248 to 302 HB, is utilised in parts including gears, shafts, studs, and bolts.
H13 Tool Steel
H13 tool steel, also known as AISI H13 or 1.2344, is a versatile and widely used hot work tool steel known for its excellent combination of properties suitable for high-temperature applications. One of the most significant properties of H13 tool steel is its excellent resistance to thermal fatigue, which makes it ideal for high-temperature applications. It can maintain its hardness and mechanical properties even at elevated temperatures, which is crucial for die-casting and forging dies.
P20 Tool Steel
P20 tool steel is a versatile, low-alloy tool steel known for its excellent plastic mold performance. It is widely used in the manufacturing of injection molds and compression molds for plastic processing applications. P20 tool steel is known by various trade names, including AISI P20, DIN 1.2311, and 718.
P20 steel is often delivered in a pre-hardened condition with a hardness of around 28-34 HRC. This pre-hardening simplifies machining and toolmaking processes, but further heat treatment is possible to achieve higher hardness when required. P20 tool steel can undergo heat treatment processes such as annealing, quenching, and tempering to achieve the desired hardness and properties.
You can drill into hardened tool steel using either a carbide bit or a diamond bit, but cooling is typically necessary. In a commercial metalworking shop, this task would likely be done using a plasma cutter or a water jet cutter.
O1 and D2 tool steels are both cold work steels used for cutting tools. D2 can achieve a finer edge, while O1 is stronger and easier to sharpen but less resistant to rust. D2, with its high chromium content, is considered semi-stainless.
Both A2 and D2 are cold work steels achieving exceptional hardness when heat-treated. A2 offers a balance of wear resistance and toughness, making it versatile. D2 prioritizes hardness and wear resistance but sacrifices some toughness.
Tool steel is hardened through a process called heat treatment, which involves heating the steel to a specific temperature, holding it there for a period of time, and then rapidly cooling it.
Tool Steel Halesowen | Manchester | Coventry | Birmingham | Kidderminster | Blackpool